Custom machining with CNC milling machine
The new and constantly changing rules of the automotive aftermarket tell us that we have to face up with two variables that work in inverse proportionality: the price drop, that more and more frequently means that a product does not meet the demand of some owners and, more generally, the worsening of spare parts that require more effort to be installed, due to imperfect dimensions. The market for tuning parts records the same trend, where lower prices give the enthusiasts only flashiness, not quality.
Making custom components with a CNC machine, such as the MAG-CX3 500, responds to the need for customization. This is where the self-construction of a wheel spacer dedicated to BMW vehicles stems from. A tailor-made work that allows the owner to decide precisely the desired widening of the car, to pick the most appropriate color and ensures the robustness of the result with specific technical characteristics of uniformity and continuity, in order to guarantee the highest standards.
The starting point was the measurement of the wheel hub with relative working measurements, attention to the wheelbase and harmonization of the joint, for a perfect match in hundredths of a millimeter of the unsprung masses on the car and realization of the the 3D model with the help of a dedicated CAD software.
The process then moved to the digital world where the various steps were taken with a design software, starting from the approval of the design, which must be supported by a detailed FEM report (Finite Element Method), the focus moves to the industrialization step that will see a CAM software as a protagonist, capable of generating tool paths that are readable and executable by a CNC milling machine. It should be underlined that for constructional needs a support jig tool was designed and built to ensure the correct clamping when working on the raw material.
The milling lasted 3 hours in order to take care of every single bevel and finishing, enhancing the characteristics of MAG-CX3 500 which - thanks to the precision and robustness given by the granite countertop (grade 2) and with a frame that minimizes vibrations and oscillations - allowed a hundredth-of-a-millimeter precise chip removal, counting moreover on the use of all the 6 tools changed in total pneumatic automation.
The final step, before installation on the car, tells us about a spacer of absolute technical value.
After closing the last bolt, it is the beauty of the car, only for track use, and the owner's happiness that guarantee the perfect outcome of this custom made spacer.
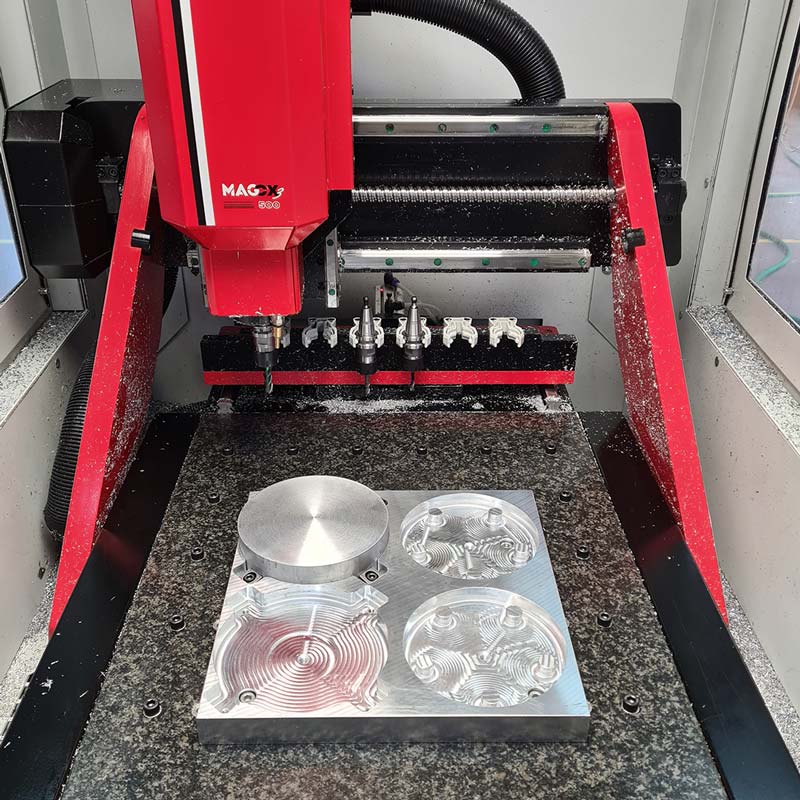
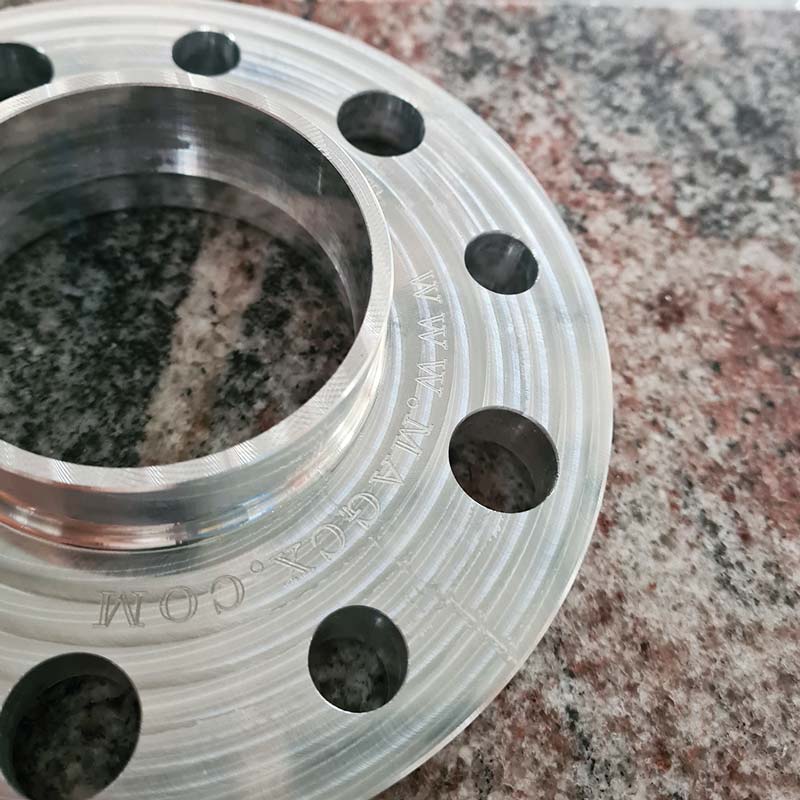
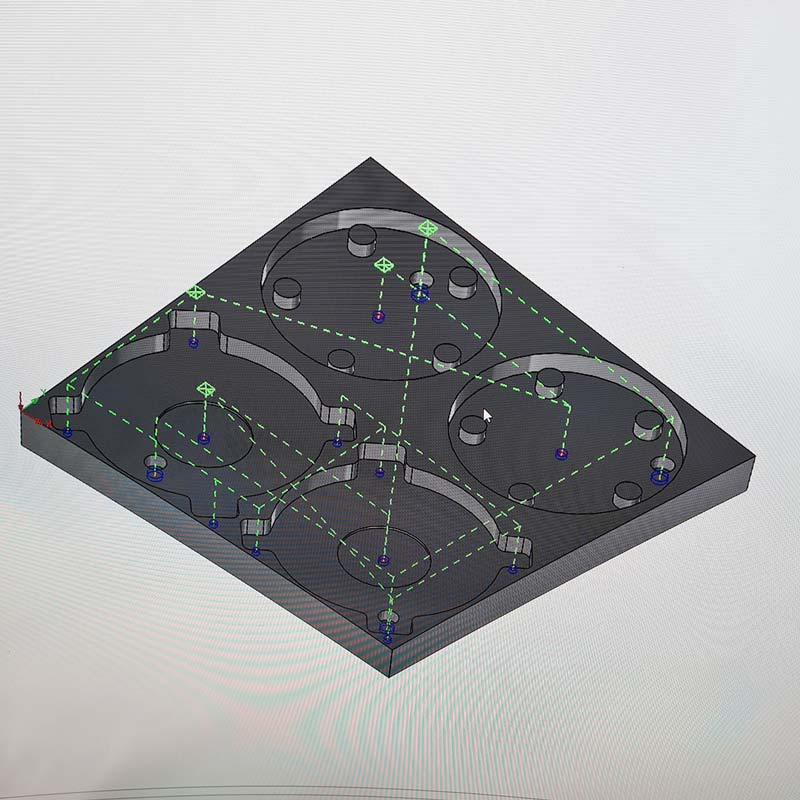
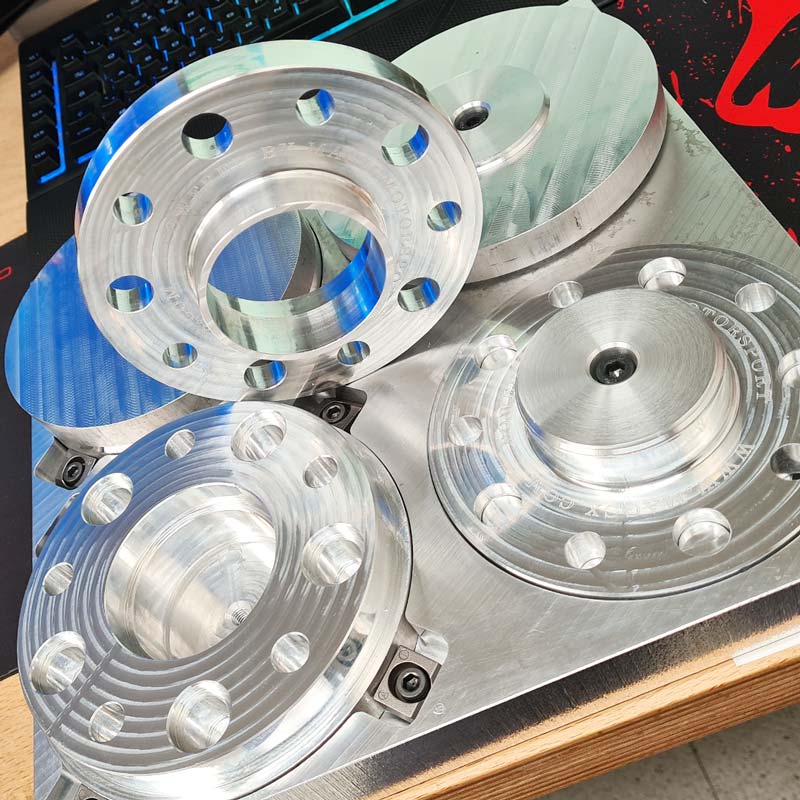